Everything You Need to Know About Investment Casting & Electromagnetic Pumps
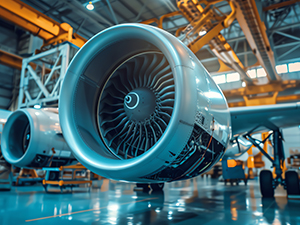
While many casting processes are capable of producing high-quality, dimensionally perfect parts, few are capable of matching the precision of investment casting. The method creates highly accurate parts with superior surface quality – and excels at casting parts with complex geometries and designs. The aerospace, automotive and medical device industries are among those that rely … Everything You Need to Know About Investment Casting & Electromagnetic Pumps